In this article, the software and hardware architecture of the Fully actuated aerial robot developed at the Robotics and Mechatronics department used for the experimental validation of the interaction control algorithms developed.
Hardware Architecture
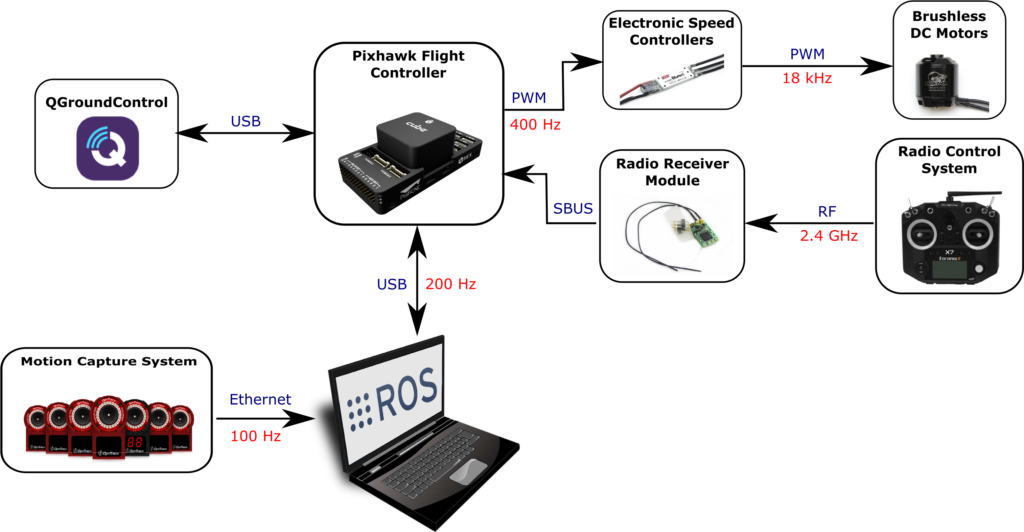
Our fully-actuated aerial robot was developed in-house based on an off-the-shelf carbon fiber frame with a diameter (rotor hub to rotor hub) of 0.68 m and a nominal total mass less than 2 kg, without batteries. For the generation of thrust, the system uses 11-inch propellers driven by six CM-2217 brushless motors with DYS SN40A electronic speed controllers. Each rotor has the capability to produce a maximum thrust of 12.5 N.
Software Architecture of Experimental Platform
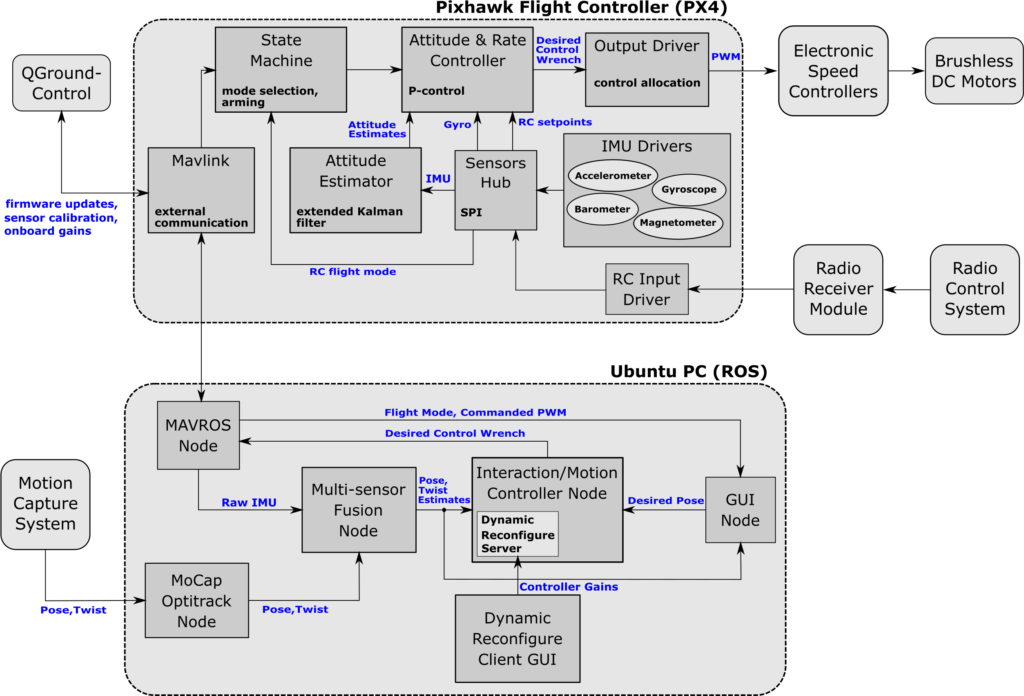
The vehicle is equipped with a Pixhawk 2.1 flight controller with integrated sensors. The Pixhawk runs the PX4 software, which handles interfacing to the sensors and actuators in addition to providing a modular framework which allows adding new control schemes. We augment the original PX4 software with custom-made modules that enables the control of fully-actuated multi-rotors. This involves modifying the PX4 control allocation module, and low-level orientation controllers. Using a multi-sensor fusion algorithm, the sensor data provided by the inertial measurement unit in the Pixhawk is fused together with the external pose information from the Optitrack motion capture system to provide reliable estimates of the UAV configuration and body twist.
Software Architecture of Software-In-the-Loop Simulation
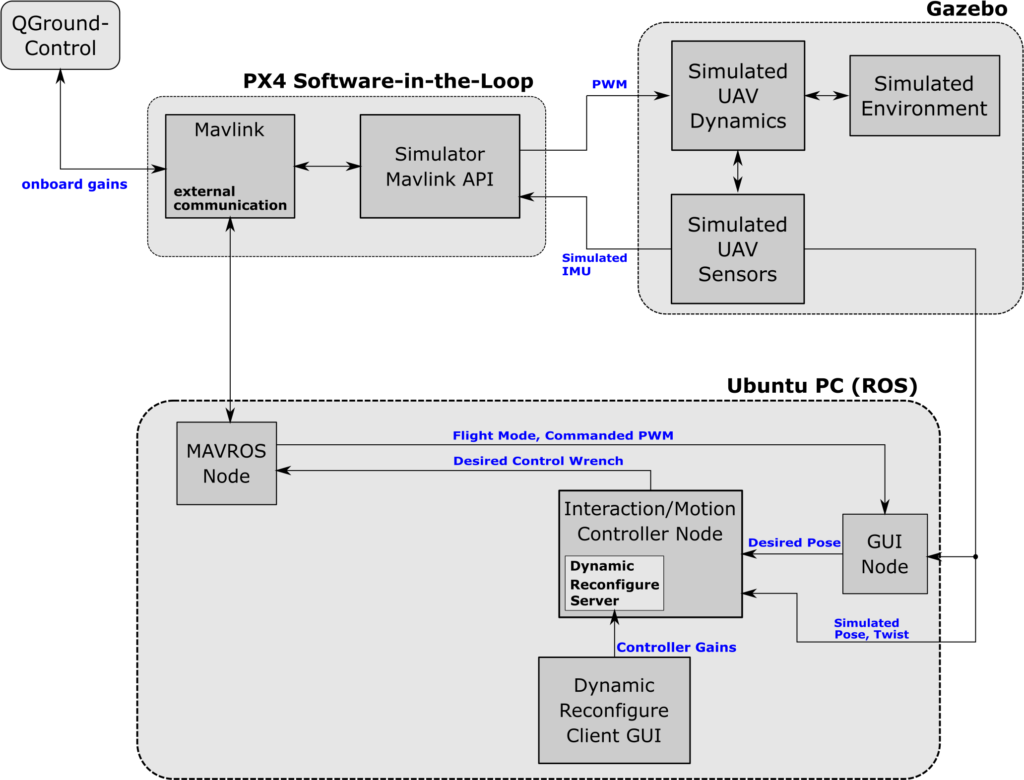
To assess the validity of our interaction control algorithms and vision-based algorithms on unknown surfaces, the overall impedance control-based interaction framework was implemented and extensively tested in a simulation environment based on Gazebo, the RotorS plugin, and a software-in-the-loop (SITL) version of the PX4 software. The SITL receives the same commands through through ROS, as the real experimental setup. This significantly reduces the time required to validate the theory with real experiments and helps with tuning the different gains present in the control system.
Parameters Identification
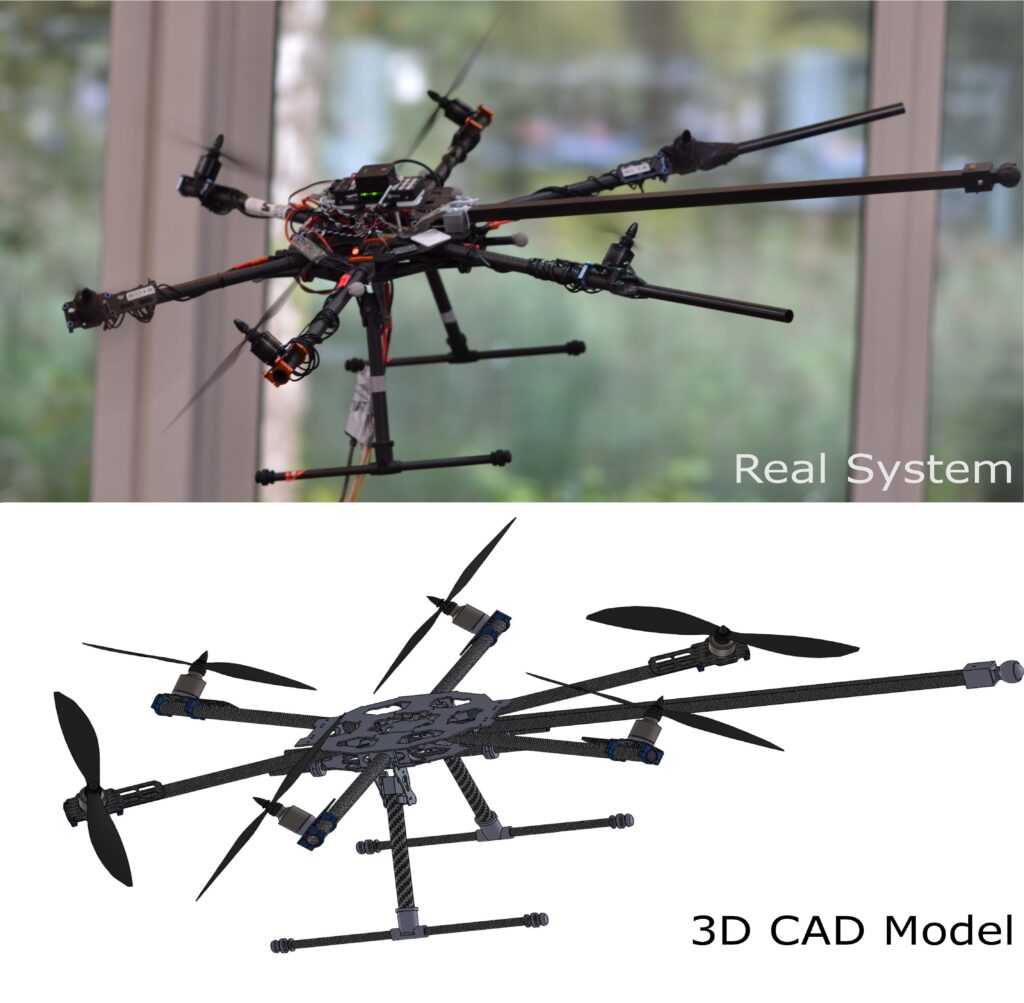
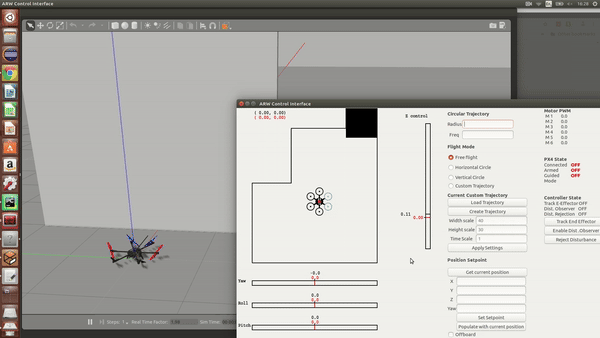
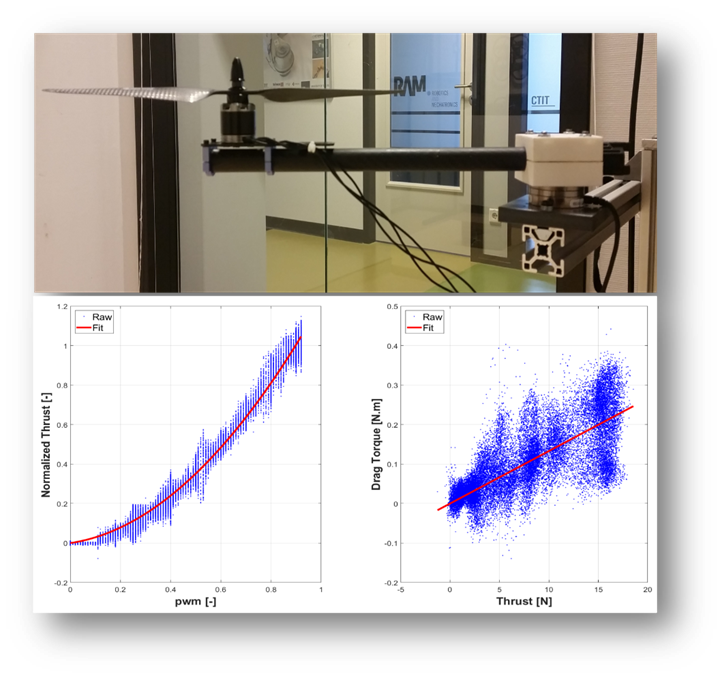